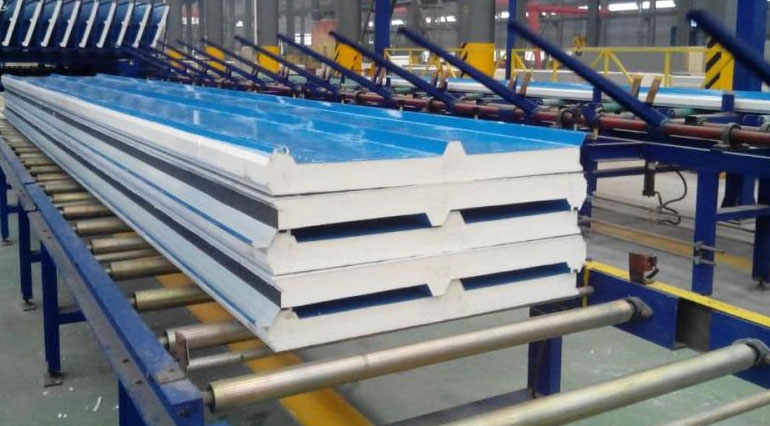
Sandwich panel
A sandwich panel, also known as a composite panel, is a type of construction material commonly used in building facades, roofing systems, and industrial applications. It consists of three layers: two outer skins or face sheets and a core material sandwiched between them.
The outer skins are typically made of durable materials such as metal (e.g., aluminum, steel), fiberglass, or reinforced plastics. These skins provide structural strength, protection against weather elements, and contribute to the overall appearance of the panel. The thickness and properties of the outer skins can vary based on the intended application and desired performance characteristics.
The core material of a sandwich panel is usually a lightweight material that provides insulation, rigidity, and additional structural support. Common core materials include expanded polystyrene (EPS), polyurethane (PU), polyisocyanurate (PIR), mineral wool, and aluminum honeycomb. The choice of core material depends on factors like thermal insulation requirements, fire resistance, acoustic performance, and mechanical properties.
The combination of the outer skins and the core material creates a sandwich-like structure, hence the name. The core acts as a separator and helps to distribute loads across the panel, increasing its strength and stiffness while minimizing its weight. This construction design makes sandwich panels efficient and cost-effective, as they offer a high strength-to-weight ratio and excellent thermal and acoustic insulation properties.
Sandwich panels have various applications in the construction industry. They are commonly used for wall cladding, partitions, roofs, and doors in both commercial and residential buildings. They are also utilized in industrial settings, such as cold storage facilities, cleanrooms, and modular construction projects. The ease of installation, versatility, and energy efficiency of sandwich panels make them a popular choice in many construction projects.